PE Pipe Production Line
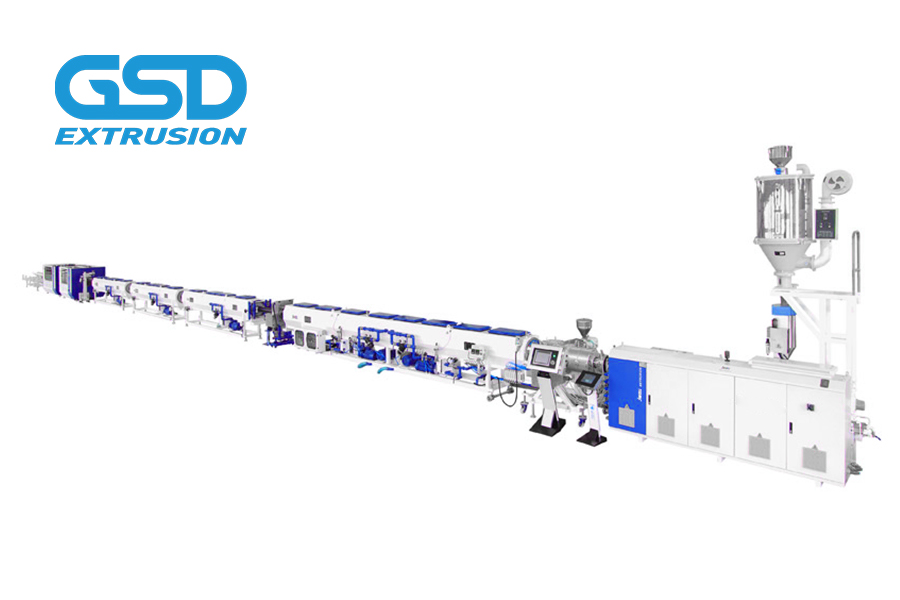
Home / PE Pipe Production Line
PE Pipe Production Line
The PE Pipe Production Line is a specialized machine used for the manufacturing of PE (Polyethylene) pipes. This production line typically includes equipment such as an extruder, a sizing unit, a cooling tank, haul-off machines, and cutting equipment. The process begins with feeding PE resin into the extruder, where it is melted and formed into a continuous pipe shape. The pipe is then sized and cooled in the cooling tank to achieve the desired dimensions and properties. Finally, the haul-off machine pulls the pipe through the line while the cutting equipment cuts it into individual lengths. PE pipes produced by this production line are widely used in various applications such as water supply, irrigation, drainage, and gas transportation due to their excellent flexibility, durability, and corrosion resistance.
What PE Pipe Production Line You Need ?
GSD extrusion which is a manufacturing vendor, specializing in the PE Pipe Production Line and spare parts, with high quality machine and competitive price.
Product Application Of PE Pipe Production Line
The raw materials for producing PE pipes are usually PE100 or PE80, and the size and performance of the PE pipes must meet the requirements of relevant international standards like ISO4427. Compared with traditional cement pipes and metal pipes, PE pipes have outstanding advantages such as good overall performance, low water flow resistance, and long service life. They have been widely used in urban water supply, urban gas supply, urban sewage systems, industrial and agricultural pipelines, and communication cable protection pipelines and other fields.
(1)PE Water Supply Pipe
- PE pipes are widely used in building water supply systems, industrial water treatment systems, and municipal water supply systems, etc. They can be used as tap water pipes, irrigation pipes and pressure water supply pipes, etc., with advantages such as convenience for transportation, resistance to chemicals, hygienic, environmentally friendly, and good flexibility.
(2)PE Silicone Core Pipe
- PE silicone core pipe for optical cable protection has a silicone solid lubricant on the inner wall. Silicone core pipes are widely used in optical cable communication network systems for railways and highways. They have the advantages of moisture-proof, insect-proof, anti-corrosion, and anti-aging. The silicone core layer on the inner wall of the pipeline does not react with water. The contaminants in the pipeline can be flushed out directly with water. The radius of curvature of the silicone core pipe is small, so it can turn along the road or follow the slope without any special treatment.
(3)PE Communication Pipe
- PE communication pipes can be used in power communication systems and perform well in the resistance to corrosion, compression, and impact.
(4)PE Gas Pipe
- The underground PE gas pipe is suitable for a gas transmission pipeline system with a working temperature ranging from -20 to 40℃ and a long-term maximum working pressure lower than 0.7MPa.
Technical highlights of GSD PE Pipe Production Line
According to the actual needs of different customers, we provide Siemens S7-1200 series PLC control system or manual control system for your option. The Siemens PLC control system with a 12-inch full-color touch screen is easy to operate. Operators can also easily control daily functions by mechanical buttons below the touch screen without taking off heat-resistant gloves. The manual control system is equipped with independent thermometers which are simple to operate and easy to maintain.
Extruder
- Our PE pipe production line is equipped with a high-performance single-screw extruder. The professionally designed single screw guarantees a superb plasticizing effect. The single screw extruder can be equipped with the German iNOEX weighing and feeding system, which is integrated with the main PLC control system, without any need to install an additional weighing terminal. It can be switched between the two control modes of “Meter Weight” and “Output”, and the raw material can be saved by 3% to 5% for long-term use. The extruder adopts a variable frequency AC motor or a permanent magnet synchronous motor with excellent comprehensive performance, which saves more than 20% of power consumption compared with a DC motor. The feed bush with the grooved inner wall is equipped with a spiral water-cooled runner, which can effectively increase the extrusion output by 30% to 40%.
Extrusion Die
- The PE pipe extrusion die adopts a spiral flow channel structure specially designed by Blesson, which can ensure the uniformity of the melt temperature, completely eliminate the melt confluence mark inside the pipe, and avoid the stripe defect caused by the basket-type die.
- The extrusion die has been treated by several processes. The melt runner is chrome-plated or nitrided, and polished, with low resistance and anti-corrosion.
- The friendly design of Blesson’s PE pipe extrusion die is convenient for users to quickly change bushes, pins, and calibrators of different sizes.
- We apply internal heating devices inside the extrusion dies for PE pipes above Ø110mm, and an internal air extraction system for PE pipes above Ø250mm to improve the pipe quality.
Vacuum Tank
- The vacuum tank body is made of high-quality SUS304 stainless steel, and the water pipeline and fittings are also all made of anti-corrosion SUS304 stainless steel, which assures a long service life.
- The vacuum tank adopts a vacuum negative pressure closed-loop system, which can automatically adjust the vacuum degree. It is highly efficient and energy-saving, and also ensures the stability of vacuum shaping, and effectively reduces noise.
- The vacuum tank has a precise automatic control system for water level and water temperature. The centralized drainage system can realize rapid water change, which helps to save time and improve its efficiency.
- The large-capacity filters can effectively block the impurities in the water, ensure the quality of the circulating water. The filters can achieve a quick manual cleaning, which is convenient for maintenance.
Spray Tank
- The spray tank can quickly cool the pipes in all directions, thus helping to increase the production line speed.
- According to the actual production need, the customer can adjust the height of the pipe support easily.
- The spray tank body, pipeline, and fittings are all made of stainless steel, which is anti-corrosion and durable.
- For small and medium-size pipe spray tanks, our company adopts a smart height adjustment device for pipe supports. Through the handwheel, the height of multiple pipe supports can be adjusted uniformly, which is convenient for customers to change the pipe size.
Haul-Off Unit
- For different pipe diameters and line speeds, our company provides belt or multi-caterpillar haul-off units for customers’ options.
- The abrasion resistance of our caterpillars is strong. And the rubber block hardly slips due to the large friction.
- Each caterpillar is controlled by a separate permanent magnet synchronous motor to ensure a wide speed range with stable hauling performance.
- The haul-off unit for large-diameter pipes can be equipped with a hoisting device (winch) for the leading pipe during the trial test.
Cutting Unit
- We have a flying knife cutting unit, planetary cutting unit, and swarfless cutting unit for customers’ options.
- The swarfless cutting unit adopts a multi-point clamping method by pneumatic, which is convenient for pipe size changeover.
- The design of both double round knives or single-pointed knives of the swarfless cutting unit ensures a smooth cut.
- The control system is equipped with an independent 7″ color touch screen, HMI + Siemens PLC integrated machine.
- The synchronization effect is stable and the cutting length is accurate.
Winding Unit
- Our company provides a variety of winding solutions such as single-station or double-station winders, and the winding speed is synchronized with the production line speed.
- The winding unit is equipped with functions such as automatic pipe laying, tension control, pipe clamping, coil pressing.
- The winding unit is driven by a servo motor with Inovance PLC+HMI control (the whole unit adopts the open bus protocol), which has high control accuracy.
- The automatic double-station bundling and the winding unit have an automatic roll change function, and can automatically strap and unload rolls. It is suitable for high-speed small pipe production lines up to 32mm.
Model List of PE Pipe Production Line
PE Pipe Production Line | |||||
Line Model | Diameter Range(mm) | Extruder Model | Max. Output(kg/h) | Length of Line(m) | Total Installation Power(kW) |
GSD-32PE(I) | 16-32 | GSD50-34 | 150 | 20 | 100 |
GSD-32PE(II) | 16-32 | GSD50-40 | 340 | 48 | 130 |
GSD-32PE(III) | 16-32 | GSD65-34 | 250 | 48 | 150 |
GSD-32PERT | 16-32 | GSD65-34 | 250 | 48 | 145 |
GSD-32PEX(I) | 16-32 | GSD65-34 | 200 | 46 | 170 |
GSD-32PE(IIII) | 6-25 | GSD65-30 | 120 | 65 | 125 |
GSD-32PE(IIIII) | 5-32 | GSD40-34 | 70 | 29.4 | 70 |
GSD-63PE(I) | 16-63 | GSD50-40 | 300 | 53 | 160 |
GSD-63PE(III) | 16-63 | GSD65-34 | 250 | 53 | 160 |
GSD-63PE(IIII) | 16-63 | GSD65-34 | 250 | 38 | 235 |
GSD-63PE(IIIII) | 8-63 | GSD50-34 | 180 | 21 | 70 |
GSD-63PE(IIIIII) | 16-63 | GSD50-40 | 340 | 38 | 165 |
GSD-110PE(I) | 20-110 | GSD50-40 | 340 | 55 | 160 |
GSD-110PE(II) | 20-110 | GSD65-35 | 350 | 55 | 180 |
GSD-160PE(I) | 32-160 | GSD50-40 | 340 | 48 | 160 |
GSD-160PE(II) | 40-160 | GSD65-40 | 600 | 59 | 240 |
GSD-160PE(III) | 32-160 | GSD80-34 | 420 | 52 | 225 |
GSD-160PE(IIII) | 40-160 | GSD65-34 | 250 | 45 | 255 |
GSD-160PE(IIIII) | 32-160 | GSD65-38 | 500 | 52 | 225 |
GSD-250PE(I) | 50-250 | GSD50-40 | 340 | 45 | 170 |
GSD-250PE(II) | 50-250 | GSD65-40 | 600 | 52 | 225 |
GSD-250PE(III) | 50-250 | GSD80-34 | 420 | 45 | 215 |
GSD-315PE(I) | 75-315 | GSD65-40 | 600 | 60 | 260 |
GSD-315PE(II) | 75-315 | GSD50-40 | 340 | 50 | 170 |
GSD-450PE(I) | 110-450 | GSD65-40 | 600 | 51 | 285 |
GSD-450PE(II) | 110-450 | GSD80-40 | 870 | 63 | 375 |
GSD-450PE(III) | 110-450 | GSD100-34 | 850 | 54 | 340 |
GSD-630PE(I) | 160-630 | GSD80-40 | 870 | 61 | 395 |
GSD-630PE(II) | 160-630 | GSD100-40 | 1200 | 73 | 515 |
GSD-630PE(III) | 160-630 | GSD120-33 | 1000 | 66 | 480 |
GSD-630PE(IIII) | 160-630 | GSD90-40 | 1000 | 66 | 450 |
GSD-800PE(I) | 280-800 | GSD120-33 | 1000 | 66 | 500 |
GSD-800PE(II) | 280-800 | GSD100-40 | 1200 | 66 | 535 |
GSD-1000PE(I) | 400-1000 | GSD150-34 | 1300 | 70 | 710 |
GSD-1000PE(II) | 400-1000 | GSD100-40 | 1200 | 70 | 710 |
GSD-1000PE(III) | 400-1000 | GSD120-40 | 1500 | 70 | 675 |
GSD-1200PE(I) | 500-1200 | GSD150-34 | 1300 | 53 | 660 |
GSD-1200PE(II) | 500-1200 | GSD100-40 | 1200 | 53 | 580 |
GSD-1200PE(III) | 500-1200 | GSD120-40 | 1500 | 60 | 670 |
GSD-1600PE | 500-1600 | GSD150-34 | 1500 | 71 | 890 |
GSD-355PE | 110-450 | GSD80-40 | 870 | 65 | 400 |
Request A Quote
If you have any questions or need assistance, feel free to reach out to us today; we are here for you 24/7. Hope to cooperate with you!
For smoother and more efficient communication, and to ensure that you receive our messages promptly, we recommend reaching out to us directly through WhatsApp or our designated Email Address. We will respond to your message as soon as possible. Typically, you can expect to receive our reply within 1-2 hours.