Lithium Battery Separator Film Production Line
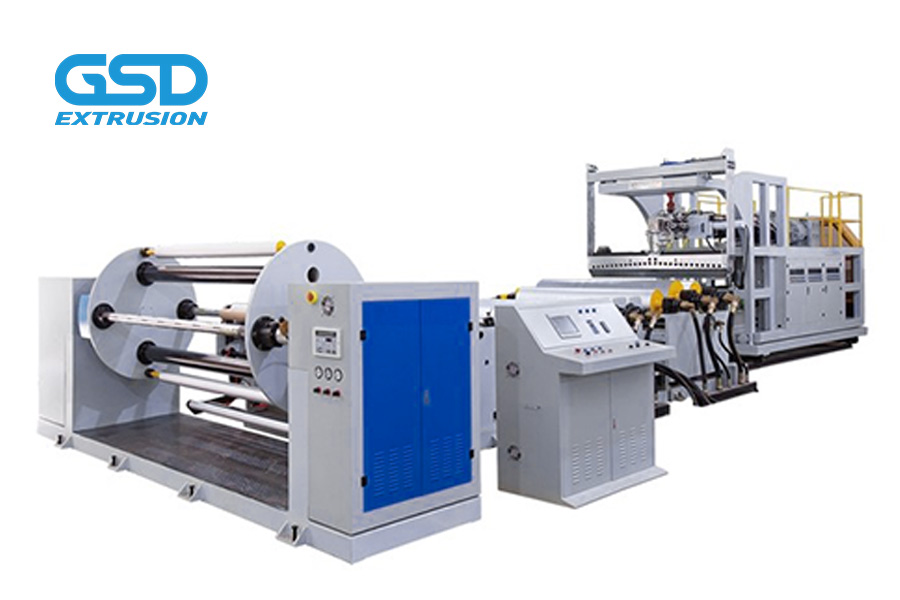
Home / Lithium Battery Separator Film Production Line
Lithium Battery Separator Film Production Line
The Lithium Battery Separator Film Production Line is a specialized machine designed for manufacturing separator films used in lithium-ion batteries. This production line typically includes extruders, a flat die, stretching equipment, and winding machinery. The process involves extruding polymer materials, such as polyethylene or polypropylene, into thin films, which are then stretched to achieve the desired porosity, thickness, and mechanical properties. Separator films play a crucial role in lithium-ion batteries by preventing short circuits between the positive and negative electrodes while allowing the flow of ions. These films contribute to the safety, efficiency, and performance of lithium-ion batteries used in various applications such as consumer electronics, electric vehicles, and energy storage systems.
What Lithium Battery Separator Film Production Line You Need ?
GSD extrusion which is a manufacturing vendor, specializing in the Lithium Battery Separator Film Production Line and spare parts, with high quality machine and competitive price.
Lithium Battery Separator Film Production Line
- Raw material: PP/PE
- Product structure: single layer or 3-layer co-extrusion
- Film weight range: 10-50 g/㎡
- Final film width: up to 1300mm
- Mechanical speed: 200m/min
Application of Lithium Battery Separator Film Production Line
Lithium batteries are widely used in our daily life products, including mobile phones, laptops, and other electronic products. With the development of new energy vehicles, the demand for lithium batteries will increase. Lithium batteries are gradually replacing traditional batteries in aerospace, navigation, artificial satellites, medical, military communications equipment, and other fields. Lithium battery separator film is the key component of the structure of lithium batteries. The film is made of plastic, which prevents direct contact between the anode and cathode to avoid the short circuit. And it also offers the ability to shut down at a temperature slightly lower than that at which thermal runaway occurs, while retaining its mechanical properties.
Main technical features
- 1. Automatic vacuum feeding and plastic/metal separation and dust removal system.
- 2. The extrusion part matches the viscosity and rheological properties of the raw material.
- 3. High precision melt filtration and melt conveying part.
- 4. Single-layer or multi-layer co-extrusion runner system and automatic die head.
- 5. Fully automatic thin film thickness measurement system integrated with production line control system.
- 6. High-performance anti-vibration casting station equipped with electrostatic/pneumatic edge pinning, vacuum box, and air knife.
- 7. Double-station turret winder:
- (1) Accurate double tension control to achieve low tension winding.
- (2) Film winding conicity optimization control system.
- (3) Without adhesive glue or adhesive tape while changing reel.
Request A Quote
If you have any questions or need assistance, feel free to reach out to us today; we are here for you 24/7. Hope to cooperate with you!
For smoother and more efficient communication, and to ensure that you receive our messages promptly, we recommend reaching out to us directly through WhatsApp or our designated Email Address. We will respond to your message as soon as possible. Typically, you can expect to receive our reply within 1-2 hours.